Plastic extrusion for pipes, sections, and custom shapes
Plastic extrusion for pipes, sections, and custom shapes
Blog Article
Recognizing the Fundamentals and Applications of Plastic Extrusion in Modern Manufacturing
In the world of contemporary production, the technique of plastic extrusion plays an important function - plastic extrusion. This detailed process, including the melting and shaping of plastic via specialized dies, is leveraged across various sectors for the development of diverse items. From auto components to consumer goods product packaging, the applications are large, and the possibility for sustainability is equally impressive. Unwinding the fundamentals of this procedure discloses real flexibility and possibility of plastic extrusion.
The Fundamentals of Plastic Extrusion Process
While it might appear complicated, the fundamentals of the plastic extrusion procedure are based on reasonably simple principles. It is a manufacturing procedure wherein plastic is thawed and after that formed right into a continuous profile via a die. The plastic extrusion procedure is extensively used in numerous markets due to its cost-effectiveness, efficiency, and versatility.
Various Types of Plastic Extrusion Methods
Structure upon the basic understanding of the plastic extrusion process, it is required to explore the various methods included in this manufacturing technique. In contrast, sheet extrusion produces big, flat sheets of plastic, which are generally more refined right into products such as food product packaging, shower drapes, and car parts. Recognizing these strategies is key to using plastic extrusion efficiently in modern-day production.

The Duty of Plastic Extrusion in the Automotive Sector
A frustrating bulk of parts in modern-day lorries are products of the plastic extrusion process. Plastic extrusion is largely utilized in the manufacturing of numerous vehicle parts such as bumpers, grills, door panels, and dashboard trim. Thus, plastic extrusion plays a pivotal duty in automotive production.

Applications of Plastic Extrusion in Customer Goods Manufacturing
Past its substantial effect on the automotive market, plastic extrusion proves equally effective in the realm of consumer goods manufacturing. This process is important in creating a broad range of products, from food packaging to household appliances, playthings, and also medical devices. The flexibility of plastic extrusion enables producers to develop and create complicated sizes and shapes with high precision and efficiency. Due to the recyclability of lots of plastics, squeezed out parts can be reprocessed, lowering waste and price (plastic extrusion). The Discover More flexibility, versatility, and cost-effectiveness of plastic extrusion make it a recommended selection for numerous durable goods makers, contributing considerably to the sector's development and advancement. Nevertheless, the environmental effects of this extensive usage need mindful factor to consider, a topic to be discussed better in the subsequent area.
Environmental Effect and Sustainability in Plastic Extrusion
The pervasive usage of plastic extrusion in producing invites examination of its environmental implications. Reliable equipment decreases power use, while waste management systems reuse scrap plastic, reducing raw material needs. In spite of these enhancements, even more technology is required to minimize the ecological impact of plastic extrusion.
Verdict
In conclusion, plastic extrusion plays an essential duty in modern manufacturing, especially in the auto and customer goods industries. Its adaptability enables for the production of a variety of elements with high accuracy. Its possibility for recycling and advancement of eco-friendly materials supplies a promising opportunity in the direction of sustainable methods, thereby attending to ecological concerns. Comprehending the fundamentals of this procedure is vital to optimizing click here now its advantages and applications.
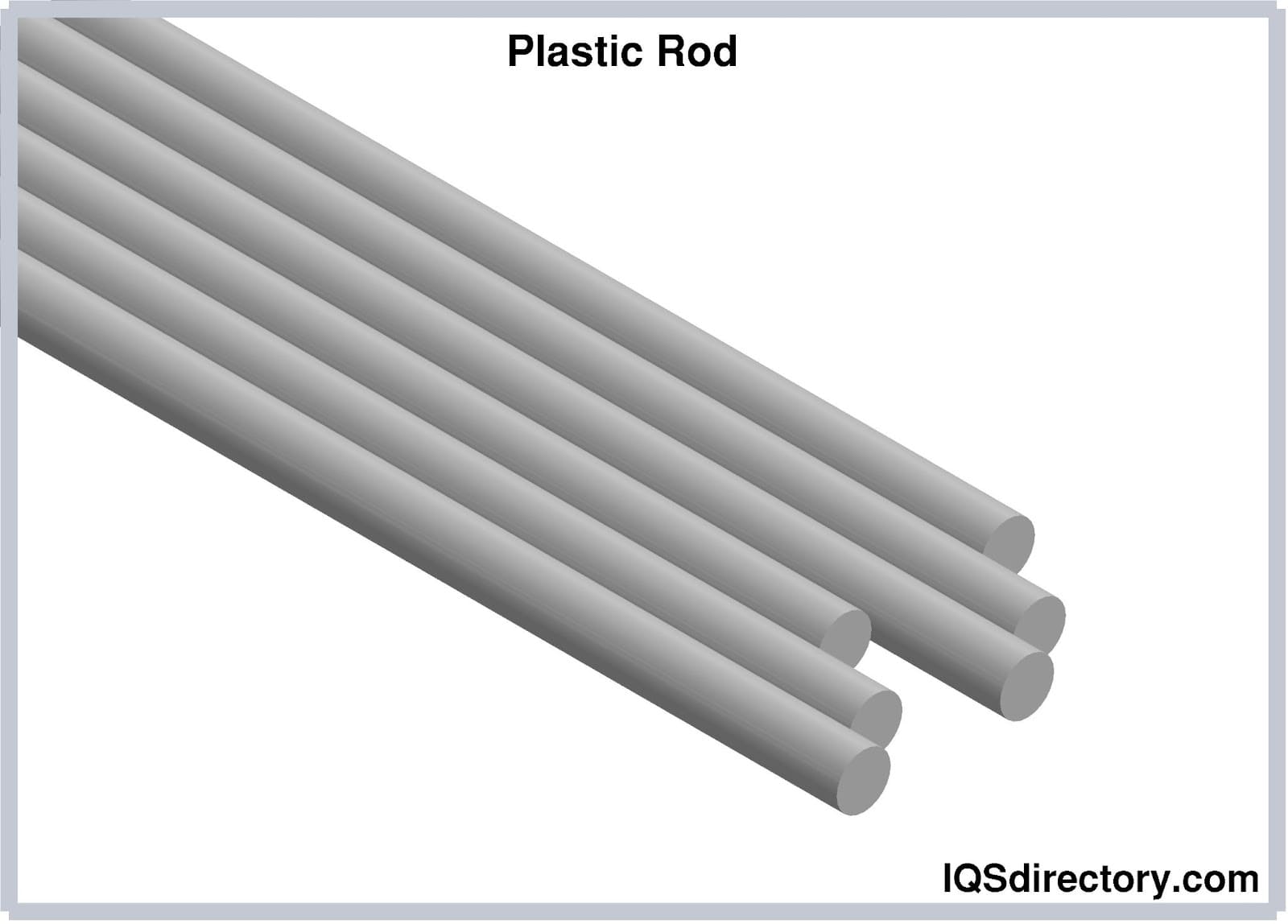
The plastic extrusion procedure is thoroughly utilized in different industries due to its performance, flexibility, and cost-effectiveness.
Building upon the basic understanding of the plastic extrusion procedure, it is read this post here needed to check out the various strategies included in this manufacturing approach. plastic extrusion. In comparison, sheet extrusion creates large, level sheets of plastic, which are generally further refined right into items such as food packaging, shower drapes, and auto components.A frustrating bulk of parts in contemporary automobiles are items of the plastic extrusion procedure
Report this page